Dive Into the Globe of Light Weight Aluminum Casting: Understanding the Different Approaches
Light weight aluminum spreading is an essential procedure in the production sector, with numerous techniques employed to develop precise and detailed elements. Understanding the different techniques made use of in light weight aluminum casting can give important understandings right into the abilities and limitations of each strategy. From the standard sand casting method to the advanced die casting procedure, each technique offers one-of-a-kind advantages depending on the needs of the project. Discovering these diverse methods can provide an extensive sight of the possibilities within the globe of aluminum casting and how each method adds to shaping the modern-day manufacturing landscape.
Sand Spreading Technique
Sand spreading, a widely-used method in aluminum casting procedures, entails developing mold and mildews made of compressed sand for putting molten metal. Once the mold and mildew is all set, it is firmly positioned in a flask and molten light weight aluminum is poured right into the cavity.
After the metal has actually cooled and solidified, the sand mold and mildew is damaged away to expose the aluminum casting. Sand spreading permits for the manufacturing of complicated shapes and big parts that might be costly or hard to create utilizing other approaches. It is additionally a sustainable strategy as the sand can be reused and utilized several times, reducing waste in the spreading process.
Long-term Mold Strategy
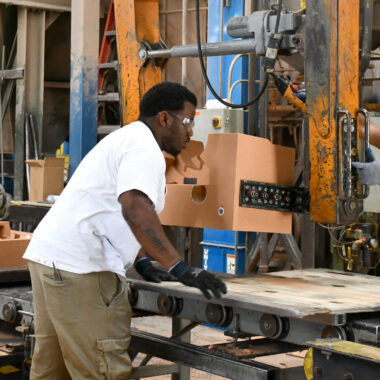
One significant advantage of the Permanent Mold Strategy is the improved dimensional accuracy it offers. The metal mold and mildew enables tighter resistances and better information in the last aluminum castings compared to sand spreading methods. This precision makes it a favored choice for applications where limited dimensional control is crucial, such as in the aerospace and vehicle sectors.

Pass Away Casting Refine
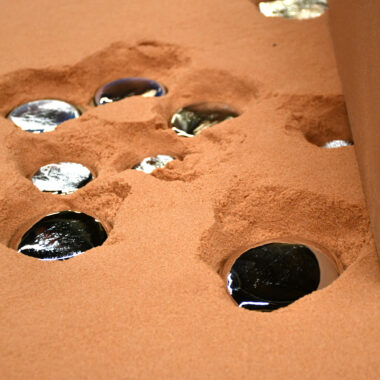
Investment Casting Method
Using a precision spreading method, Investment Casting Strategy includes creating detailed light weight aluminum components by pouring molten steel into a ceramic mold and mildew. This process, additionally known as lost-wax spreading, begins with the creation of a wax pattern of the preferred part (aluminum casting).
Investment spreading is typically utilized for making components in markets where tight tolerances and complex layouts are required, such as aerospace, auto, and medical equipment. The adaptability and accuracy of the Financial investment Casting Approach make it a useful strategy in the world of aluminum casting.
Lost Foam Casting Technique
Having explored the elaborate precision of Investment Casting Technique, the emphasis currently changes to the ingenious method of Lost Foam Casting in aluminum component manufacturing. Lost Foam Casting, also referred to as evaporative pattern casting, is a contemporary method where a foam pattern of the preferred part is created and after that index covered with a refractory product. The covered foam pattern is after that buried in sand, and molten aluminum is poured right into the mold and mildew. As the steel fills up the mold, the foam evaporates due important link to the warmth, leaving a tidy dental caries in the form of the preferred part.
Among the major benefits of Lost Foam Spreading is its capability to produce intricate shapes with intricate information, commonly in a solitary item without the requirement for additional machining. This approach is likewise recognized for its high dimensional accuracy and smooth surface area finish. Additionally, Lost Foam Spreading is an economical process as it lowers the demand for cores and permits the production of light-weight components. Regardless of its advantages, Lost Foam Spreading needs careful control of the spreading process to protect against problems and ensure quality parts.
Verdict
To conclude, aluminum spreading supplies a variety of techniques such as sand spreading, irreversible mold and mildew technique, die casting, financial investment spreading, and lost foam casting. Each method has its own benefits and applications, making light weight aluminum casting a versatile and widely utilized procedure in numerous industries. Understanding the differences in between these techniques is crucial in selecting the most appropriate casting method for certain manufacturing needs.
Sand spreading, a widely-used technique in light weight aluminum spreading procedures, entails developing mold and mildews made of compressed sand for putting molten metal. aluminum casting.The Long-term Mold Technique, like sand casting, is one more common technique utilized in aluminum casting procedures, supplying distinctive benefits in terms of mold and mildew reusability and dimensional precision. The steel mold enables for tighter resistances and better details in the final aluminum spreadings contrasted to sand spreading methods. The 2 major kinds of die casting are cold chamber die casting and her response hot chamber die casting, each suitable for various kinds of aluminum alloys.In conclusion, light weight aluminum spreading uses a range of methods such as sand casting, irreversible mold and mildew method, pass away casting, financial investment spreading, and lost foam casting
Comments on “Reinvent Your Production with Aluminum Casting Innovations”